
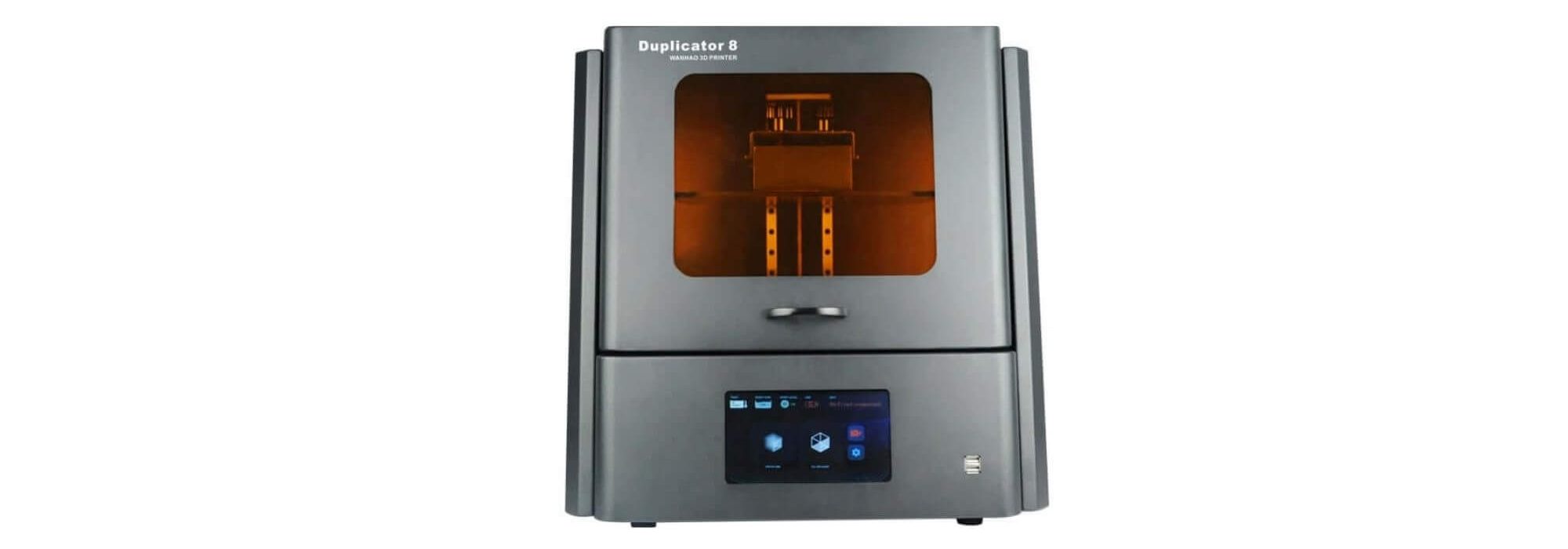
- #Repetier server and wanhao duplicator 4s drivers
- #Repetier server and wanhao duplicator 4s pro
- #Repetier server and wanhao duplicator 4s software
- #Repetier server and wanhao duplicator 4s professional
#Repetier server and wanhao duplicator 4s pro
It runs Repetier Server Pro with a webcam. I use the raspberry pi method for controlling all my devices. I have friends actually using OctoPrint on a Pi for their 3d printer without an issue as well.
-1-750x930.jpg)
I have a air scrubber which cleans the air at the attic, to catch what is not caught by my dust shoe, it has a timer so I can let it run for another hour after the milling has strange that you get corrupt SD-Cards, the Raspberry PI which I use to run GRBLweb is hard cycled all the time and has not corrupted in over 2 years now.Normally when your bag fills up the suction gets less. I have a Cyclone installed which catches the milling dust in a separate bin and thus keeps your expensive vacuum bags clean and therefore your shopvac suction on it’s max.
#Repetier server and wanhao duplicator 4s professional
#Repetier server and wanhao duplicator 4s drivers
But this has the stepper drivers and laser driver directly hooked up to the arduino. I do have a Laser Engraver as well, an older own design and build which I have running GRBL and I control via a Raspberry with GRBLWeb, which I really find a nice way of controlling the machine remote.
#Repetier server and wanhao duplicator 4s software
Yes I’m sticking with Marlin, since I’m not a hardware software wizard, so just wanted to stick to the paved ways. That’s really nice to have, so it shuts up when it’s done.īe sure to post what you end up Thanks for your input. You should also consider controlling the spindle power with something. Maybe instead focus on getting some hearing protection with builtin headphones and a good list of podcasts. I’ve left it running for little spurts during the cut though.

There is also a fire risk, if chips build up, they can catch fire, although I think that’s sort of rare. Then stopping the cut, or fixing a binding cable or something. I’ve saved more than a few boards by being there when something went wrong. I doubt anyone would say it is “safe” to leave the machine alone. The web interface is my only way of jogging the machine under power.Īnother important note is that CNC machines are more dangerous than printers (IMO), and they fail quite quickly. I can load gcode files from my laptop, and if I set up the mpeg streaming, then I can see the USB video in the web interface. I did get a webcam working on the webpage, and I put in a request to the author to add hooks for starting and stopping timelapses, but I never tested his/her fix. It’s a bit behind the octopi in terms of setup, etc. With that setup, I run CNC.js, and I can do a little management. I switched to a GRBL controller built into the pi, and I don’t know if anyone else is doing that (and Ryan won’t be any help there, since he’s focused on Marlin for good reasons). Also, the octoprint issue trackers are pretty good, so you can report problems with it there. I bet most of that is just as compatible as Marlin. There might be some gcode that confuses it (G00 vs G0 or (comments) vs. The only possible gotchas are the temps and the gcode viewer won’t work (It ignores travel, I think). I have an octopi, and some experience with it, if you get stuck. Octopi is the easiest way to get started.
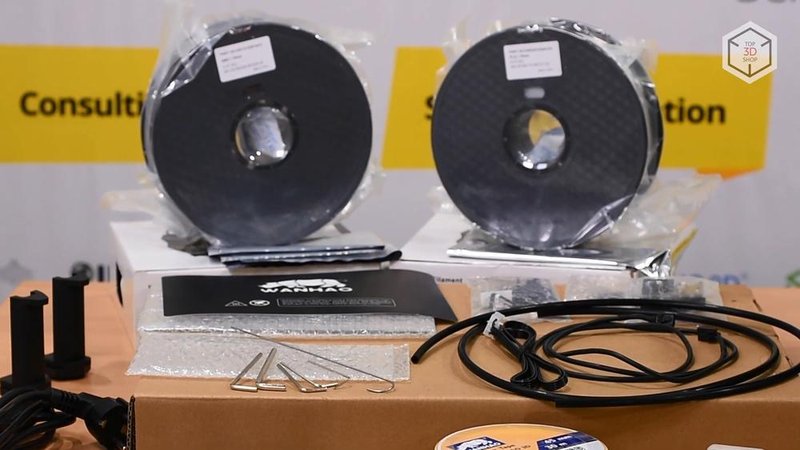
If you can get octoprint to work, I think that’s the best option. If you’re staying with the Marlin firmware, I think you’ve nailed the choices. I think I promised to look into octoprint a really long time ago… Sorry, I got distracted and when I got back, I went to GRBL.
